Chemical Resistance is the ability of the polymer to resist an attack from certain chemicals for a specific period of time while maintaining its physical and mechanical properties. Materials with poor chemical resistance when exposed will see a drop in mechanical properties, causing blistering, swelling and cracking, as the polymer becomes non functional in a short duration.
The molecular structure of the polymer, the additives added along with the solvents and chemical reagent concentration, exposure time, and temperature are the primary variables determining chemical resistance.
The rate of chemical attack is reduced by crystallization, fillers, and cross-links and increased by the presence of plasticizers or in contact with solvents. Polymers are more readily attacked by corrosives at temperatures above the glass transition temperature,Tg. Chemical resistance is enhanced by the types and quality of polymers, plasticizers and additives included in the resin/compound formula.
It’s essential to evaluate the environment in which a plastic will function in order to choose the right option for a specific application. The following aspects should be taken into account:
- Chemicals- acids,bases, solvents, hydrocarbons,etc.
- Concentration of chemicals
- Operating Temperature
- Life span of application
- Thickness of film
- Additional mechanical constraints
In order for a polymer to maintain its mechanical qualities and function at its best over an extended period of time, several factors are crucial. But even chemically inert plastics, or those that exhibit a wide range of pH and chemical type resistance, won’t be able to withstand all chemical agents. Therefore, in order to select the proper polymer and guarantee its chemical compatibility, it is crucial to examine the agent(s) in question.
Table of Contents
Main types of chemical products that normally come in contact with polymers can be listed below:
- Acids (hydrochloric acid, sulfuric acid, nitric acid) pH < 7
- Bases (baking soda, soap, bleach, ammonia) pH > 7
- Solvents and alcohols(methanol, ethanol, acetone)
- Hydrocarbon fuels (gasoline, jet fuel)
Below are some of the most popular Polymers that have good chemical resistance.
PVC (polyvinyl chloride)
PVC is commonly used in the commercial roofing’s, geomembranes, primary and secondary containment liners, oil booms, bio gas tank covers, protective garments and covers. The chemical resistance of PVC is dependent of the type and plasticizer used, as some plasticizers have better chemical resistance than others. Not all PVC is created equal, at e2we offer a variety of single ply and reinforced PVC products.
EIA (Ethylene interpolymer alloy)
Ethylene interpolymer alloy (EIA), also known as Elvaloy or KEE (ketone ethylene ester), has earned a lot of acceptance in the primary and secondary containment geomembrane market as a result of its better chlorine resistance.DuPont/DOW developed KEE to provide a solid plasticizer or polymer to replace liquid plasticizers that would make PVC and other polymers flexible without concerns of plasticizer migration and loss leading to improved chemical resistance over plasticized PVC. e2XTRM PLY HP, HPL, HPLX and ER 1000 are designed to meet some of the most challenging chemical requirements.
EPS Geofoam is becoming increasingly important as a lightweight alternative to soil andgravel when used as structural backfill in highways, bridges, embankments, and parking lots but the Geofoam is not compatible with petroleum products. e2 has developed XTRM Ply EPSWrap which has very good chemical and hydrocarbon resistance to protect the Geofoam from potential exposure from fuel or chemical spills.
TPU (Thermoplastic Poly Urethane)
TPU’s chemistry will determine how it performs in specific environments, as a general rule Polyether TPU’s are considered to have good hydrolysis resistance, where as Polyester TPU’s have good resistance oils, fuels and chemicals. At e2 we offer a variety of coated fabric offering for potable water, loading docks, inflatables, oil booms and many more markets, more information is available at e2 TPU Coated Fabrics website.
LLDPE (Linear Low-Density Polyethylene)
The polyethylene (HDPE, LDPE, and LLDPE) family is chemically compatible with many chemicals and resistant to strong acids and bases. The polyethylene resins (PEs) have an extremely high resistance to chemicals and other media because of their non-polar nature. Aqueous solutions of salts, acids, and alkalis have no effect on it. PEs are not resistant to strong oxidizing agents such as nitric acid, fuming sulfuric acid, or halogens. High-density polyethylene is a material that is well known for being robust, stable, and simple to weld. It also exhibits outstanding resilience to acidic solutions. e2 offers string reinforced LLDPE composite membrane up to widths of 10 ft in 30, 36 and 45 mil thickness primarily used in the geomembrane industry.
PP (polypropylene)
PP is resistant to chemicals and stress cracks. Made from the olefin propylene, polypropylene (PP) is a thermoplastic polyolefin that is chemically inert. As a result, it can be utilized in applications involving direct contact with food. It has a high level of resistance to common chemicals. Polypropylene is also used for outdoor applications like terraces, patios, roofing and liners. At E Squared we offer reinforced PP which are used in applications like floating covers and water containment.
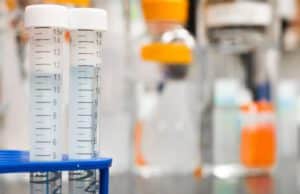
Testing for Chemical Compatibility
Testing for polymer chemical resistance assures that interactions between polymers and the chemicals won’t lead to disastrous failures or malfunctions. At E Squared we examine a broad range of characteristics that might be impacted by fluid interactions, such as mechanical strength, elongation, swelling, chemical deterioration and weight change.
Some of the common test methods usually accepted for chemical resistance are:
- ASTM D1239-22 -Standard Test Method for Resistance of Plastic Films to Extraction by Chemicals
- ASTM D543-21 – Standard Practices for Evaluating the Resistance of Plastics to Chemical Reagents
- ASTM D5747/D5747M-21 -Standard Practice for Tests to Evaluate the Chemical Resistance of Geomembranes to Liquids
Most the tested methods involve immersion of the polymer or polymer composited in the chemical at either room temperature or at elevated temperatures for a set duration and evaluating the properties before and after exposure, the common test involve:
- Changes in mass/volume/ dimensions
- Mechanical properties – Tensile strength, Elongation, Tear resistance
- Compression and bending properties
- Immersion testing (days to months)
- Change in Hardness
- Visual Appearance
At E Squared, we offer a variety of polymers and test for many of the chemicals that are present in operational settings as part of our chemical resistance program, which are listed in our Chemical Resistance chart, for additional testing and data please contact our Technical and Sales Team.
References:
- Ouellet-Plamondon, C. M., Sami Rtimi, & Phuong Nguyen Tri. (2019). Nanomaterials-Based Coatings: Fundamentals and Applications. Elsevier.
- Ammar, Sh., Wonnie Ma, I. A., Ramesh, K., & Ramesh, S. (2019). Polymers-based nanocomposite coatings. Nanomaterials-Based Coatings, 9–39. https://doi.org/10.1016/b978-0-12-815884-5.00002-8
- Seymour, R.B., Carraher, C.E. (1984). Chemical Resistance of Polymers. In: Structure—Property Relationships in Polymers. Springer, Boston, MA. https://doi.org/10.1007/978-1-4684-4748-4_10
- Sastri, V. R. (2010). Commodity Thermoplastics. Plastics in Medical Devices, 73–119. https://doi.org/10.1016/b978-0-8155-2027-6.10006-6
- PolyAlto, G. (n.d.). Which plastics are resistant to chemicals? Blogue.polyalto.com. Retrieved August 30, 2022, from https://blogue.polyalto.com/en/plastics-resistant-to-chemicals
- Polymer Chemical Resistance Testing. (n.d.). Element. Retrieved August 30, 2022, from https://www.element.com/materials-testing-services/polymer-testing-services/polymer-chemical-resistance-testing
- ASTM D1239, 2014, “Standard Test Method for Resistance of Plastic Films to Extraction by Chemicals”,ASTM International, DOI: 10.1520/D1239-14
- ASTM D543, 2021,” Standard Practices for Evaluating the Resistance of Plastics to Chemical Reagents”, ASTM International, DOI: 10.1520/D0543-2
- ASTM D5747/D5747M,2021, “Standard Practice for Tests to Evaluate the Chemical Resistance of Geomembranes to Liquids”, ASTM International, DOI: 10.1520/D5747_D5747M-21
- (2019, June 1). Clarifying the nomenclature of Elvaloy-based geomembranes: EIA, EIP or KEE. Geosynthetics Magazine. https://geosyntheticsmagazine.com/2019/06/01/clarifying-the-nomenclature-of-elvaloy-based-geomembranes-eia-eip-or-kee/